Saturday, May 13, 2017
Craft of Political Graffiti in Chennai
No comments:
Labels:
Chennai,
graffiti,
painting,
political graffiti,
politics,
street art,
wall painting
Street art, with its focus on images and artistry, has become a primary mode of public expression in international metropolises and a global language for citizens to articulate sociopolitical criticisms all the while expressing individual artistry. When one walks through the streets of Chennai, it is hard to miss the street art that colour the walls. From bold Tamil slogans to portraits of politicians, Chennai exhibits a different culture of street art. The concept of street art or graffiti has evolved over time in every aspect. Themes, motivations, mind sets and tools have changed with time. Interestingly, street art in Chennai is a perfect blend of the traditional with the modern and the local with the global.
It is often said that politics is the art and technique of government. Every idea has an intention, similarly political idea also has the intention for implementation, but many people see this with negative mindset. It includes the activities to stay in power or to influence the government policies. It also includes the law- making policies and procedure. Political parties are indispensable for the working of modern democratic governments. The importance of Political parties lies in the fact that democracies cannot function without the existence of political parties.
For years now the canvas of the artist has been expanding. One no longer has to limit oneself to the boundaries of paper or cloth. The walls of the cityscape with their ever-widening horizons have turned into the media on which several artists choose to project their creativity. While there is no formal definition of street art, one can introduce this practice as one where artists leave behind their impressions on walls. Using paint brushes, cans of spray-paint, stencils, fingers, hands, and the like, as instruments, they mark the walls, either casually, or with political intentions; and sometimes the walls simply become an outlet for their creativity. One could associate it with a child doodling on her first blank sheet of paper.
While graffiti has traditionally been highly controversial, the advent of iconographic street art has opened new platforms for international youth to creatively express sociopolitical discontent. Ironically, Indian artists have been using graffiti like techniques for ages, right from store name boards and signages to movie posters and public service announcements, so the actual “influence” per se was to voice opinions about what may be considered taboo in the once conservative society of India. Indian artists such as Daaku, (also known as the Indian Banksy), are inspired to create and voice out common dillemas and current affairs, in public places and more.
Before the age of televisions and broadcast, the sole method of public awareness were wall paintings. With the vibrant and standard party associated colors, the party and the artist intended to create associative cognitive learning from spectating the grafffiti that illustrates the concerned parties colors, representatives name and style Tamil Nadu Graffiti stands apart from the regular kind globally with its incorporation of typography, colors and visual hierarchy.
The previous DMK-led corporation council spent nearly 4.5 crore to paint nearly 15 lakh sqft of walls with murals depicting among other things rural life, shore temples of Mamallapuram and the Vivekananda Rock. Last year, the AIADMK-led council whitewashed all walls and is now clueless about what to do with them. Earlier, it planned to paint the government’s achievements on them.
But a casual gaze at the abandoned walls, street corners and even the beaches in the city, reveals a colourful blend of political portraits, vibrant graffiti and even modern art, created by those who are mostly called perpetrators of vandalism a.k.a. the street artists of Chennai.
While the poorer neighbourhoods in the city mostly contain political portraits and graffiti, as one moves down south towards the more affluent part of the city, the politicians and their various moods captured on enamel are replaced with spray paintings that are mostly an expression of angst by the angry, young city artist.
In the northern suburb of Ayanavaram, Chennai resides Mr. Kalai Cholai an artist by profession and a philosopher by night. He specialises in the art of wall painting and practises the same without any bias. He is humble, kind and wise as he tell me (an aspiring artist myself) how painting the shabby wall gives him spiritual peace of mind and keeps his skills trained. “Its all about scales” he says.
The design process begins with the client or the company the artist works on a tenure period with a party giving the artist an assigned artwork for a wall along with its dimensions. .Soon after that , the artist plans his scale and and the specifics of the image/ typography to be painted on. According to Mr. Kalaicholai an experienced artist’s sometimes do not use the grid and prefer free hand drawing, however the less experienced amateur artists use the ruler and grid plans to verify scaling.
The artist now evauates and budgetises the project and requests for it followed by receiving the same and spending it on the project. The artist now does a simple white was with putty to get the desired and apt background . They then paint sketch over the background post drying and paint it in. Once the first layer is done, the artist makes necessary changes, color corrections, and gradations .
note: the thickness/ number of coats of paints varies from wall to wall, i.e the grainier, the more layers and graffiti wont be considered as vandalism as long as the owner of the wall is awake and approving of it.
Read More
It is often said that politics is the art and technique of government. Every idea has an intention, similarly political idea also has the intention for implementation, but many people see this with negative mindset. It includes the activities to stay in power or to influence the government policies. It also includes the law- making policies and procedure. Political parties are indispensable for the working of modern democratic governments. The importance of Political parties lies in the fact that democracies cannot function without the existence of political parties.
While graffiti has traditionally been highly controversial, the advent of iconographic street art has opened new platforms for international youth to creatively express sociopolitical discontent. Ironically, Indian artists have been using graffiti like techniques for ages, right from store name boards and signages to movie posters and public service announcements, so the actual “influence” per se was to voice opinions about what may be considered taboo in the once conservative society of India. Indian artists such as Daaku, (also known as the Indian Banksy), are inspired to create and voice out common dillemas and current affairs, in public places and more.

The previous DMK-led corporation council spent nearly 4.5 crore to paint nearly 15 lakh sqft of walls with murals depicting among other things rural life, shore temples of Mamallapuram and the Vivekananda Rock. Last year, the AIADMK-led council whitewashed all walls and is now clueless about what to do with them. Earlier, it planned to paint the government’s achievements on them.
But a casual gaze at the abandoned walls, street corners and even the beaches in the city, reveals a colourful blend of political portraits, vibrant graffiti and even modern art, created by those who are mostly called perpetrators of vandalism a.k.a. the street artists of Chennai.
While the poorer neighbourhoods in the city mostly contain political portraits and graffiti, as one moves down south towards the more affluent part of the city, the politicians and their various moods captured on enamel are replaced with spray paintings that are mostly an expression of angst by the angry, young city artist.
In the northern suburb of Ayanavaram, Chennai resides Mr. Kalai Cholai an artist by profession and a philosopher by night. He specialises in the art of wall painting and practises the same without any bias. He is humble, kind and wise as he tell me (an aspiring artist myself) how painting the shabby wall gives him spiritual peace of mind and keeps his skills trained. “Its all about scales” he says.
The design process begins with the client or the company the artist works on a tenure period with a party giving the artist an assigned artwork for a wall along with its dimensions. .Soon after that , the artist plans his scale and and the specifics of the image/ typography to be painted on. According to Mr. Kalaicholai an experienced artist’s sometimes do not use the grid and prefer free hand drawing, however the less experienced amateur artists use the ruler and grid plans to verify scaling.
The artist now evauates and budgetises the project and requests for it followed by receiving the same and spending it on the project. The artist now does a simple white was with putty to get the desired and apt background . They then paint sketch over the background post drying and paint it in. Once the first layer is done, the artist makes necessary changes, color corrections, and gradations .
note: the thickness/ number of coats of paints varies from wall to wall, i.e the grainier, the more layers and graffiti wont be considered as vandalism as long as the owner of the wall is awake and approving of it.
Wednesday, May 3, 2017
Coconut Shell craft
No comments:
Labels:
Coconut Shell craft,
Crafts of South India,
eco friendly,
home decor,
Pondicherry,
thengai mattai
Traditionally, crafting objects out of coconut shell to make household objects was practiced by coconut farmers. They would scoop out the copra by making a neat hole at the top of the shell, and use the shell, which was the waste or by-product.
It is believed that as a craft, coconut shell/wood carving could have been experimented with by craftsmen from the Vishwakarma community in Kerala. Traditionally involved in sword making and carving wood and ivory, they may have tried out coconut wood and shell as well.
Coconut shell and wood craft is primarily prevalent in Kerala: in and around Calicut, Trivandrum, Attingal, Neyyatinkara and Quilandy in Kozhikode. Other states where this craft is practiced are Goa, the Andaman and Nicobar Islands and a few parts of Bengal, Pondicherry and Tamil Nadu. Another instance of availability of coconut shell craft is in the tribal belt of Bastar where intricately designed patterns in white metal are inlayed in the shell and cut to make bangles
This craft is also prevalent in other countries such as Cambodia, Thailand, the Philippines, Java, Maldives and Sri Lanka.
Kavin crafts is group of artisans from Pondicheery India,manufacturing eco friendly handmade products.Kavin’s Craft has a small production unit with a lathe machine and a vertical drilling machine.
Read More
It is believed that as a craft, coconut shell/wood carving could have been experimented with by craftsmen from the Vishwakarma community in Kerala. Traditionally involved in sword making and carving wood and ivory, they may have tried out coconut wood and shell as well.

Coconut shell and wood craft is primarily prevalent in Kerala: in and around Calicut, Trivandrum, Attingal, Neyyatinkara and Quilandy in Kozhikode. Other states where this craft is practiced are Goa, the Andaman and Nicobar Islands and a few parts of Bengal, Pondicherry and Tamil Nadu. Another instance of availability of coconut shell craft is in the tribal belt of Bastar where intricately designed patterns in white metal are inlayed in the shell and cut to make bangles
This craft is also prevalent in other countries such as Cambodia, Thailand, the Philippines, Java, Maldives and Sri Lanka.
Kavin crafts is group of artisans from Pondicheery India,manufacturing eco friendly handmade products.Kavin’s Craft has a small production unit with a lathe machine and a vertical drilling machine.

Documented by Prateek Amber
Tuesday, May 2, 2017
Tamil Epigraphy
Epigraphy or incision of text on a hard surface like clay tablet,metal plate or a rock was a common practice for keeping literary records in all popular civilisations from Indus valley in the east to the Mayan civilisation in the west. Ever since the beginning of the human history, literary sources are considered to be the most valuable and reliable sources of information. Although in Indian subcontinent, there are evidences of written manuscripts which dates back to 1000BCE, but some archeologist believes that the languages used in these manuscripts are derivates of an older, much simpler parent language. While the ancient manuscripts from Indus valley is still to be decoded properly, the two oldest recognisable language from Indian subcontinent are Sanskrit and Tamil, written in various scripts like Dravidian, Devanagari, Brahmi and Prakrit. While Sanskrit was dominant in the North- Western part of the Indian subcontinent, Tamil dominated the South-Eastern part of it. Tamil is the oldest subcontinental language which is spoken till date. It has evidences to be found at around 300 BCE.
During the Pandyan rule of around 1200 years, the Thamizh script had changed drastically and is still going through a lot of of changes. The city of Madurai, which has long been the Pandyan capital is the best place to visit, to know the evolution of Tamil script. The inscription at Samanar malai has from 4th century AD in “vattezhuthu” has Jain aesthetic where as the inscription on the walls of eastern gate of Meenakshiamman temple has inscriptions which is from 12th century AD is quite similar to modern Tamil.
These Tamil epigraphs showed us how a script can play an major role in evolving a language over a course of time. These manuscripts also made us realise how important the art and skill of epigraphy was. Epigraphy is currently no longer practiced but this skill based art is the reason why we know what we know about our history.
Documented by Kritarth Ghosh
Read More

After the Vedic era, the Indian subcontinent was divided into various small kingdoms based on their clans. South India was predominantly ruled by three major clans, the Chola, The Chera and the Pandyas. All three of them were Tamil speaking warrior clans and ruled the entire South India from 300 BCE to 11th century AD. The Cholas were the largest kingdom of south India and were excellent artisans, architects and traders; but they were the Pandyas who patronised “Sen Thamizh” or pure Tamil as their official language for all their literature and accounts. Unlike the Cholas who used Tamil -Brahmi as their writing scripts, Pandyas incorporated “vattezhuthu” or cursive writing in their script which had an Jain aesthetic to it. This gave them an upper hand in exploring to write on various new materials such as clay tablets and metal plates as it became easier to write without damaging the surface. Also it made their writings last much longer.

These Tamil epigraphs showed us how a script can play an major role in evolving a language over a course of time. These manuscripts also made us realise how important the art and skill of epigraphy was. Epigraphy is currently no longer practiced but this skill based art is the reason why we know what we know about our history.
Documented by Kritarth Ghosh
Thursday, March 9, 2017
Amazing Wood carving in chennai
Wood carving is found all over India. We can see carved wooden pillars and doorways in temples and palaces across the country.and now, wood carving is mostly found in functional articles like furniture, bowls, boxes, lamp stands, etc. Depending on the availability, different types of woods were used for wood carving, and for making decorative wood installations. The origins of the craft can be traced back to the late 19th century which is Closely associated with architecture, wood carving incorporated the design vocabulary of architectural carvings.
HOW TO GET STARTED
First Select wood that is appropriate size and shape. For bigger art pieces more than one piece of wood can be used. Always Softer wood is easier to carve, but will also get damage easier. Then next is shaping process which is done using gouge of various sizes. The gouge is a curved blade that can remove large portions of wood smoothly.For harder woods, the sculptor may use a chisel and mallet, similar to a stone carver. For making Smaller sculptures they use knife and for making larger pieces they might require the use of a saw. No matter what wood is selected or tool used, the wood sculptor must always carve either across or with the grain of the wood, never against the grain. Once the general shape is made, the carver starts using variety of chisels for creating details. They use a V tool for making fine lines or decorative cuts.The finer polishing is done with abrasive paper. After completing the carving ad finishing the artist starts sealing and coloring the woods using various natural oils inorder to protect those woods from dirt and moisture. They use gloss varnish to get a shiny surface. And then they will do a final coating with a layer of wax which protects the wood and gives shiny soft lustrous sheen
Types of tools used for wood carving is as follows
1. The carving knife: a specialized knife used to pare, cut, and smooth wood.
2. The gouge: a tool with a curved cutting edge used in a variety of forms and
3. The coping saw, a small saw that is used to cut off chunks of wood at once.
4. The chisel, large and small, whose straight cutting edge is used for lines and cleaning up flat surfaces.
5. The V-tool used for parting, and in certain classes of flat work for emphasizing lines.
6. The veiner: a specialized deep gouge with a U shaped cutting edge.
sharpening equipment, such as various stones and a strop, necessary for maintaining edges.
ABOUT THE ARTISAN
MR. Ram Bhaskar is 42 year old wood carving art craftsman comes from a family of traditional craftsmen in uttar pradesh. While his forefathers carved ivory and sandalwood. Ram mostly uses palm wood. He has a experience of 38 years and works opposite max store, near tvs showroom, at Kottivakkam in ECR, chennai.
Read More

First Select wood that is appropriate size and shape. For bigger art pieces more than one piece of wood can be used. Always Softer wood is easier to carve, but will also get damage easier. Then next is shaping process which is done using gouge of various sizes. The gouge is a curved blade that can remove large portions of wood smoothly.For harder woods, the sculptor may use a chisel and mallet, similar to a stone carver. For making Smaller sculptures they use knife and for making larger pieces they might require the use of a saw. No matter what wood is selected or tool used, the wood sculptor must always carve either across or with the grain of the wood, never against the grain. Once the general shape is made, the carver starts using variety of chisels for creating details. They use a V tool for making fine lines or decorative cuts.The finer polishing is done with abrasive paper. After completing the carving ad finishing the artist starts sealing and coloring the woods using various natural oils inorder to protect those woods from dirt and moisture. They use gloss varnish to get a shiny surface. And then they will do a final coating with a layer of wax which protects the wood and gives shiny soft lustrous sheen

Types of tools used for wood carving is as follows
1. The carving knife: a specialized knife used to pare, cut, and smooth wood.
2. The gouge: a tool with a curved cutting edge used in a variety of forms and
3. The coping saw, a small saw that is used to cut off chunks of wood at once.
4. The chisel, large and small, whose straight cutting edge is used for lines and cleaning up flat surfaces.
5. The V-tool used for parting, and in certain classes of flat work for emphasizing lines.
6. The veiner: a specialized deep gouge with a U shaped cutting edge.
sharpening equipment, such as various stones and a strop, necessary for maintaining edges.

ABOUT THE ARTISAN
MR. Ram Bhaskar is 42 year old wood carving art craftsman comes from a family of traditional craftsmen in uttar pradesh. While his forefathers carved ivory and sandalwood. Ram mostly uses palm wood. He has a experience of 38 years and works opposite max store, near tvs showroom, at Kottivakkam in ECR, chennai.
Documented by Krishna Soman
Tuesday, March 7, 2017
Serial Light Cutout Craft
No comments:
Labels:
art installation,
Chennai,
craft,
Cutout Craft,
lighting,
Serial Lights,
street art
The craft of serial light cutout is being practiced in many parts all over the world, Tamilnadu among them has the most significance for the craft. This craft is a part of the culture in Tamilnadu, The practice of Serial light cutouts began when kollywood stepped into commercial phase, movies were made to make money. Movies moved on from art to commercial, during this phase hero worship spread rapidly among fans, which turned the fans, as well as the stars, turn into rivals. Fans made paintings of their actor in gigantic sizes in theaters to show off that their actor is the best among all.
Paintings were made by splitting the image into many small pieces, painted separately and put in a structure which holds them together. But it was only visible in daylight, to make it also visible in night fans decided to use serial light cutouts which gloriously stood out in theaters during evening shows. From this point, this art of making cutouts from serial lights was made commercial. For the same reasons, this crafts was used in temple festivals and political party meetings. It acted an indication for the event which happened in that place.
The process of this crafts begins with sourcing bamboos which are already cut and ready to use. The required image is scaled and divided into parts using grids, The floor in the workshop have grids engraved which make the construction of bamboo grid easier. The image is sketched on the floor and grid constructed over them. Thinner strands of flexible bamboos are used to make the outlines and serial lights are fixed on them. Once various parts are created it is put together in the structure constructed. The artisans are electricians who also possess the aesthetic knowledge, the craft not necessarily goes on from father to child, but anyone interested can take up the craft. Materials used are bamboos, serial lights and GI wires to secure them. Currently, the craft is facing rapid development as it is used for many events.
Location of the workshop – Porur
Artisan – Hari
Contact - 09840561225
Documented by S V Aravindh Raj
Read More
The process of this crafts begins with sourcing bamboos which are already cut and ready to use. The required image is scaled and divided into parts using grids, The floor in the workshop have grids engraved which make the construction of bamboo grid easier. The image is sketched on the floor and grid constructed over them. Thinner strands of flexible bamboos are used to make the outlines and serial lights are fixed on them. Once various parts are created it is put together in the structure constructed. The artisans are electricians who also possess the aesthetic knowledge, the craft not necessarily goes on from father to child, but anyone interested can take up the craft. Materials used are bamboos, serial lights and GI wires to secure them. Currently, the craft is facing rapid development as it is used for many events.
Location of the workshop – Porur
Artisan – Hari
Contact - 09840561225
Documented by S V Aravindh Raj
Monday, March 6, 2017
Chola Pith Craft
Chola Pith is a kind of plant that grows in water. It is generally found
in abundance in tanks, lakes and swamps in South India. After removing
the impurities by washing it in water, clean pith is obtained through
which several artists find it very fascinating and pleasing to the eye
which are manufactured as images, structures, temple gopurams and
mandapams. The patronage of the public is requested to make it a
flourishing Cottage Industry.
Post the naxal period in Bengal, once after the social scenario was stabilized, people slowly started celebrating Durga Pooja at an extremely normal scale and did not have the affordability to invest in it. During this time, the idols became the reflection of their own state of mind and hence they kept their ornamentation minimalistic and pure white in Chola or Shola Pith ( as referred to in Bengal) reflecting the image if single Bengali women in a cotton ‘tant’ saree. The ornamentation done to the Durga idol done in shola pith, is knows as ‘Daak er saaj’ and considered to be the purest and indegenious forms of ornamentation. It exceeds a simplicity and ornamentation that of a woman rightly respected who everyone can connect with , such is the respect and admiration that people of Bengal havefor Goddess Durga. This is the period when Shola Pith ‘Daak er Saaj’ became known and is still practiced in many parts of Bengal, it being the traditional craft ornamentation for religious purpose.
In the present time, we still find normal clusters not only in Bengal but also in the southern part of the country who still practice this craft and make it very famous among the young generations. Coming down to Tamil Nadu in the south from West Bengal, this beautiful while milky craft is still practiced in a normal town of Kumbakonam. This town is 265 kms away down south from Chennai and is reached by travelling via Trichy and Tanjavur by train or bus.
Mr.Chokkalingam, who plays a major role in keeping the craft alive among the younger generations and making this place known for the making and the manufacturing of this craft. His workshop“Prakasam Pith works” is located at a walking distance on the 16/25 Head Post Office Road nearby to the Kumbakonam Railway Junction. A National Award winner in 1985, titled as THE MASTER CRAFTSMAN IN PITH by the Ministry of Textiles, Government of India in Madras, he has elevated this craft to a next level and today, he is known as the only person who practiced this craft in the state only as he started his practice at the age of 10. He talks about the craft, he tells us how much of skill it needs to attain perfection.
The raw materials that are used to make the end product are long branches of the Chola Pith, along with different knives and fevicol as an adhesive. The main raw material is the Chola Pith and the only process to carve out the pith is by knife. There are different names given to the Pith based on the geographical location. It is called as “netti” in Tamil, ‘bendu’ in Telugu and ‘Kadachi’ in Malayalam. The pith is green in the beginning which is easily available in water and is cleaned properly. It is first dried in the sun for a week after removing it from the water and then it is removed and cleaned well with a cloth. The pith has a tiny hole in the between for the water to pass through it and so it has a natural shine when the pith is cut through the central hole. The monuments or the buildings are made by cutting the pith in rectangular pieces and joining them together by fevicol and carving out the desired design. Previously, the mixture of flour, but presently only fevicol is used. The pith is originally off white but it can be coloured based on the customer’s demand.
The time duration of the carving process depends upon the size ,shape and the number of days depending upon the desired design. The time taken for the normal designs to be made are two to four days whereas for bigger monuments, the carving process takes place for fifteen days. The sizes vary from four inches to two feet in height and the price is based on the size.
This was an entirely beautiful experience altogether from travelling to meeting new people, experiencing the food in Kumbakonam, but this industry sometimes also has faced a lot of drawback in the sales due to the decrease in obtaining the raw materials. As the main raw material comes from the very natural element water, and as it was available in abundance 20 years ago , there was no such problem faced by the industry. But now due to the scarcity of water in the river Kaveri, in Tamil Nadu, the raw materials are now found in Rajahmundry, Andhra Pradesh and face a major problem in the delivery of the product and the sales market. But now that it has a strong base, it promises to get better each time in the matter of sales and delivery and make this industry grow bigger.
Contact:
Mr.Chokkalingam
Prakasam Pith works
16/25 Head Post Office Road, Kumbakonam
Documented by Tanvi Desai
Read More

Post the naxal period in Bengal, once after the social scenario was stabilized, people slowly started celebrating Durga Pooja at an extremely normal scale and did not have the affordability to invest in it. During this time, the idols became the reflection of their own state of mind and hence they kept their ornamentation minimalistic and pure white in Chola or Shola Pith ( as referred to in Bengal) reflecting the image if single Bengali women in a cotton ‘tant’ saree. The ornamentation done to the Durga idol done in shola pith, is knows as ‘Daak er saaj’ and considered to be the purest and indegenious forms of ornamentation. It exceeds a simplicity and ornamentation that of a woman rightly respected who everyone can connect with , such is the respect and admiration that people of Bengal havefor Goddess Durga. This is the period when Shola Pith ‘Daak er Saaj’ became known and is still practiced in many parts of Bengal, it being the traditional craft ornamentation for religious purpose.
In the present time, we still find normal clusters not only in Bengal but also in the southern part of the country who still practice this craft and make it very famous among the young generations. Coming down to Tamil Nadu in the south from West Bengal, this beautiful while milky craft is still practiced in a normal town of Kumbakonam. This town is 265 kms away down south from Chennai and is reached by travelling via Trichy and Tanjavur by train or bus.

Mr.Chokkalingam, who plays a major role in keeping the craft alive among the younger generations and making this place known for the making and the manufacturing of this craft. His workshop“Prakasam Pith works” is located at a walking distance on the 16/25 Head Post Office Road nearby to the Kumbakonam Railway Junction. A National Award winner in 1985, titled as THE MASTER CRAFTSMAN IN PITH by the Ministry of Textiles, Government of India in Madras, he has elevated this craft to a next level and today, he is known as the only person who practiced this craft in the state only as he started his practice at the age of 10. He talks about the craft, he tells us how much of skill it needs to attain perfection.
The raw materials that are used to make the end product are long branches of the Chola Pith, along with different knives and fevicol as an adhesive. The main raw material is the Chola Pith and the only process to carve out the pith is by knife. There are different names given to the Pith based on the geographical location. It is called as “netti” in Tamil, ‘bendu’ in Telugu and ‘Kadachi’ in Malayalam. The pith is green in the beginning which is easily available in water and is cleaned properly. It is first dried in the sun for a week after removing it from the water and then it is removed and cleaned well with a cloth. The pith has a tiny hole in the between for the water to pass through it and so it has a natural shine when the pith is cut through the central hole. The monuments or the buildings are made by cutting the pith in rectangular pieces and joining them together by fevicol and carving out the desired design. Previously, the mixture of flour, but presently only fevicol is used. The pith is originally off white but it can be coloured based on the customer’s demand.
The time duration of the carving process depends upon the size ,shape and the number of days depending upon the desired design. The time taken for the normal designs to be made are two to four days whereas for bigger monuments, the carving process takes place for fifteen days. The sizes vary from four inches to two feet in height and the price is based on the size.
This was an entirely beautiful experience altogether from travelling to meeting new people, experiencing the food in Kumbakonam, but this industry sometimes also has faced a lot of drawback in the sales due to the decrease in obtaining the raw materials. As the main raw material comes from the very natural element water, and as it was available in abundance 20 years ago , there was no such problem faced by the industry. But now due to the scarcity of water in the river Kaveri, in Tamil Nadu, the raw materials are now found in Rajahmundry, Andhra Pradesh and face a major problem in the delivery of the product and the sales market. But now that it has a strong base, it promises to get better each time in the matter of sales and delivery and make this industry grow bigger.
Contact:
Mr.Chokkalingam
Prakasam Pith works
16/25 Head Post Office Road, Kumbakonam
Documented by Tanvi Desai
Sunday, February 26, 2017
Shadow play of leather puppets
No comments:
Labels:
bommalattam,
Chennai,
Crafts of South India,
leather puppets,
puppetry,
puppets,
shadow puppets,
storytelling
Story telling has always been a part of humans since time immemorial. Starting from the cave paintings, man has always been interested in narrating and listening to stories. Mr. A. Selvaraja is one such inspiring person who comes from a family that holds a legacy of an ancient art, Leather puppets (or shadow puppets).
Thol bommalatam or shadow puppet is said to be one of the oldest crafts of India. Shadow puppets are flat colourful puppets, made from leather, which are operated against the rear of a tightly stretched white cloth. They are pressed against the cloth with strong source of light behind it and handled with thin bamboo sticks stuck to them. The arms have movable joints so that they can be moved in a specific way.The puppeteer holds the puppet by the lower end of the bamboo stick with one hand, and with a stick in the other hand, they manoeuver the puppet to perform the desired movements. It usually takes around 8 to 10 people to conduct the puppet show, a few for handling the puppets and the rest for playing music. His family has been a part of this art form for nearly a century. He was born into a family of puppeteers, where his ancestors are said to have been puppeteers at the court of the Sarafoji kings of Tanjore.
Preparing the leather puppets is a tedious process, that often takes a couple of days to make even the smallest of the lot. The puppets were considered to be a priced possession. Earlier, the puppets were made of deer skin and painted with natural organic dyes, which were considered to be the most valuable. The skin is treated in the sun for hours and the pulled and stretched. The process in repeated a couple of times until the leather becomes translucent so as to allow the light to pass through it.
Puppetry that started as a court entertainment exclusively for royalties, slowly started coming out for the view of general public. Ramayana was the first ever story to be performed on the shows. Later, different stories like Harichandra, Pragalath were performed at the cause of teaching morals to people especially children. When the British rule took over India, the puppeteers were left to fend for themselves. They started moving from place to place pitching tents in one village after the other and performing for the locals. They would often settled in the villages for months, met new people, made friends and left a piece of their heart as they left. Their life was a beautiful adventure every other month.
All this slowly started coming to an end, as television started blooming and one day it totally swept of the puppetry. Presently, Mr. Selvaraja is sadly one among a very few people in the state to perform and make leather puppets. He performs in Dakshin Chitra for tourists every weekend, for four shows per day. He manipulates the plot of the story every week according to important current events.
Contact :
Mr. A. Selvaraja Naidu,
No.211, pillar kovil big street,Kolathur village,
via vandalur-mambakkam,
kanchipuram district
Mobile No.- 09444671029
Dakshin Chitra puppet show timings - 11am, 12am, 3pm and 4pm (every weekend)
Read More
Thol bommalatam or shadow puppet is said to be one of the oldest crafts of India. Shadow puppets are flat colourful puppets, made from leather, which are operated against the rear of a tightly stretched white cloth. They are pressed against the cloth with strong source of light behind it and handled with thin bamboo sticks stuck to them. The arms have movable joints so that they can be moved in a specific way.The puppeteer holds the puppet by the lower end of the bamboo stick with one hand, and with a stick in the other hand, they manoeuver the puppet to perform the desired movements. It usually takes around 8 to 10 people to conduct the puppet show, a few for handling the puppets and the rest for playing music. His family has been a part of this art form for nearly a century. He was born into a family of puppeteers, where his ancestors are said to have been puppeteers at the court of the Sarafoji kings of Tanjore.

Preparing the leather puppets is a tedious process, that often takes a couple of days to make even the smallest of the lot. The puppets were considered to be a priced possession. Earlier, the puppets were made of deer skin and painted with natural organic dyes, which were considered to be the most valuable. The skin is treated in the sun for hours and the pulled and stretched. The process in repeated a couple of times until the leather becomes translucent so as to allow the light to pass through it.

![]() |
Gearing up for a show |
Contact :
Mr. A. Selvaraja Naidu,
No.211, pillar kovil big street,Kolathur village,
via vandalur-mambakkam,
kanchipuram district
Mobile No.- 09444671029
Dakshin Chitra puppet show timings - 11am, 12am, 3pm and 4pm (every weekend)
Saturday, February 25, 2017
Banana Fibre weaving at Anakaputhur
India is a land where people believed on Nature largely - used Plants as a source for medicines, food, garments etc. As time went by, people changed to using different combinations of fibres, artificial fibres. Now the cycle is back to going green. Global warming is a major threat to mankind and the world is slowly moving towards Eco-Fashion. And this is turning to be a beneficial one for the whole of weaving industry sector.
Banana fiber is one among the few fibres which has been widely used for making garments in recent years. In India, approximately 5 lakh tonnes of Banana trunk is discarded as waste every year, after harvested. India is one of the leading producers of Banana in the world. Fibre can be extracted from the trunks of Banana. Also, Banana grows faster than other plants which makes them easily available. Banana fibre, infact, is one of the most useful products in Indian Market.
Anakaputhur is one of the places where Banana fibre is used extensively in the making of garments and household products. Anakaputhur is a suburb of Chennai that lies on the banks of Adyar. Anakaputhur was once famous for its traditional weaving business, which has declined due to modern competition, this place seems to bursting it seams, unable to cope up with rapid urbanisation. Anakaputhur with its lost name, is now gaining fame for a small eco-friendly initiative.
For the last 15 years, C Shekar, a weaver, has been quietly making fabrics out of vazhai naaru (banana fibre), inspired by the traditional weavers of Philippines. Sekar is famous for his works and brings together 12 self-help women groups under the banner of AJWA to extract banana fibre, turn it into yarn and weave yardage and sarees. With a population of about 25,000, Anakaputhur has only 750 handloom weavers today. Its decreasing in recognition and that is why this part of the city needs attention.
The extraction of fibre from Banana requites care to avoid damage. Banana plant sections are cut from the stem of the plant and rolled lightly to remove the excess moisture. Impurities in the rolled fibre are removed manually by means of comb and then is cleaned and dried. Once its dried, the banana sheaths are picked out and succulent flesh is scraped off with quick strokes till the fibres are visible.
To make it as a yarn, the extracted threads of varying sizes are dried
and knotted to make it usable on a handloom. After this, the yarn is
handed over to the weavers. Once it reaches the weavers, it is spun into
a bobbin. The threaded bobbin is placed in water until it can be used
on the loom. It is inserted into the wooden shuttle that is passed
through the silk or cotton wrap, making the banana fibre yarn the weft
in the loom. The dyeing can be done in two stages: either as yarn or
after the fabric is woven, and in artificial dyes or natural ones.
In recent years, the commercial value of Banana fibre has increased and Anakaputhur plays an important role in it. It is used all over the world for various purposes for making tea bags and sanitary napkins to currency notes and car tyres. Banana stem, hitherto considered waste is now being made into banana-fibre cloth which comes in differing weights and thickness.
The reducing number of people practising this craft has left a void for the next generation to take up this craft. The people working have been provided with low wages which is affecting the craft.
Contact: C Shekar
Documented by Ajay Kumar
Read More
Banana fiber is one among the few fibres which has been widely used for making garments in recent years. In India, approximately 5 lakh tonnes of Banana trunk is discarded as waste every year, after harvested. India is one of the leading producers of Banana in the world. Fibre can be extracted from the trunks of Banana. Also, Banana grows faster than other plants which makes them easily available. Banana fibre, infact, is one of the most useful products in Indian Market.

Anakaputhur is one of the places where Banana fibre is used extensively in the making of garments and household products. Anakaputhur is a suburb of Chennai that lies on the banks of Adyar. Anakaputhur was once famous for its traditional weaving business, which has declined due to modern competition, this place seems to bursting it seams, unable to cope up with rapid urbanisation. Anakaputhur with its lost name, is now gaining fame for a small eco-friendly initiative.
For the last 15 years, C Shekar, a weaver, has been quietly making fabrics out of vazhai naaru (banana fibre), inspired by the traditional weavers of Philippines. Sekar is famous for his works and brings together 12 self-help women groups under the banner of AJWA to extract banana fibre, turn it into yarn and weave yardage and sarees. With a population of about 25,000, Anakaputhur has only 750 handloom weavers today. Its decreasing in recognition and that is why this part of the city needs attention.


The reducing number of people practising this craft has left a void for the next generation to take up this craft. The people working have been provided with low wages which is affecting the craft.
Contact: C Shekar
Documented by Ajay Kumar
Friday, February 24, 2017
Sandalwood Lace Garland
No comments:
Labels:
Chennai,
Chintadripet,
craft,
garland,
lace,
lace garland,
sandalwood,
sandalwood garland
Playing the perfect host is an integral part of the Indian culture and tradition. As such, Indian people go to great lengths to make their guests feel welcome There are basically two reasons behind the garlanding tradition of India. Firstly, it showcases one's happiness at receiving the particular guest and secondly, it is a form of publicly acknowledging the guest's importance. The fact that apart from guests, it's only the various gods and goddesses, who are garlanded, shows the significance attached to this garlanding tradition in India. In the olden days, people welcome their guests with flower garland as flowers were soft and they had a pleasant smell. People were into making flower garland as it was sold on a daily base until today the garland makers are mostly found outside the temples as people bought them to garland the Gods every time they visited. About thirty years back slowly the flower garlands were going out of trend as people started to realize that flowers from the garland were slowly falling petal by petal and also they got dried over night and people couldn’t wear it or keep it over a day. Another major problem was transportation. Garlanding statues were also a problem as they had to keep changing it every day.
Lace garlands came into the trend as it was easy to transport it from place to place and it became a status symbol for them to welcome their guests with these lace garlands. To make it look more appealing small rolls of sandalwood was made into a chain and placed as rows in between the garland.
The sandalwood garlands are expensive compared to the other garlands. This tradition was carried out for about 30 years. The makers were situated in Tanjore and they slowly emerged towards the main cities and started practicing the making of sandalwood garlands. This craft, in the beginning, evolved in Karnataka as the state had rich growth of sandalwood trees. Sandalwood grows mainly in India in the state of Karnataka. The state accounts for about 70 percent of the production, the rest mainly coming from Tamil Nadu and Andhra Pradesh. The tree grows naturally, in fertile, tropical forestlands with abundant rainfall. It is also cultivated. The tree is a root parasite. Soon after germination, the seedling finds a host and derives nourishment from it. It grows about 10 meters high, has a girth of one-and-a-half- meters and lives for over a 100 years. Today the sandalwood rolls are still bought from Tanjore as they are the major supply hub in terms of quality and quantity.
In Chennai, the making of this craft is majorly found in the areas like Chindadripet, Mylapore and Parrys. The dealers are mostly found in Parrys. Chintadripet was originally called as Chinna Thari Pettai which is a locality in Chennai, in India. Located on the southern banks of the Cooum River, it is a residential-cum-commercial area surrounded by Chepauk, Island Grounds, Pudupet, Egmore and Anna Salai.Ritchie Street, the electronic hub of Chennai, is located in Chintadripet. One more thing that the area is famous for and to not forget will be the fish market that is situated right in the middle. This serves as a perfect landmark to any location in that area.
In about 400 meters from the market at Arunachalam street “Annamalai Lace Garland” shop is situated and they are the 1st and the traditional makers of the Sandalwood Lace garlands in Chennai. They source their raw materials from Tanjore including the sandalwood, laces, and zari. It takes about 3 hours for them to make a lace garland. In a day they make about 50 garlands of different verities. They also customize according to peoples color and design choice. Annamalai lace garland is currently run by Mr.Muthu Kumar the son of Mr.Venugopal. This business has been carried out over traditions, The shop is named after his grandfather Mr.Annamalai who initially was making flower garlands in the same lane outside a temple and slowly moved on to making artificial and lace garlands. Mr.Muthu lives down the lane along with his family and is a passionate devotee of lord Shiva.
Contact:
To know more and to experience the making of this craft live visit No.89 Arunachalam street, Chindadripet, Chennai-600002. Ph- 9566065345
Document by Poornima Ramesh
Read More
Lace garlands came into the trend as it was easy to transport it from place to place and it became a status symbol for them to welcome their guests with these lace garlands. To make it look more appealing small rolls of sandalwood was made into a chain and placed as rows in between the garland.
The sandalwood garlands are expensive compared to the other garlands. This tradition was carried out for about 30 years. The makers were situated in Tanjore and they slowly emerged towards the main cities and started practicing the making of sandalwood garlands. This craft, in the beginning, evolved in Karnataka as the state had rich growth of sandalwood trees. Sandalwood grows mainly in India in the state of Karnataka. The state accounts for about 70 percent of the production, the rest mainly coming from Tamil Nadu and Andhra Pradesh. The tree grows naturally, in fertile, tropical forestlands with abundant rainfall. It is also cultivated. The tree is a root parasite. Soon after germination, the seedling finds a host and derives nourishment from it. It grows about 10 meters high, has a girth of one-and-a-half- meters and lives for over a 100 years. Today the sandalwood rolls are still bought from Tanjore as they are the major supply hub in terms of quality and quantity.

Contact:
To know more and to experience the making of this craft live visit No.89 Arunachalam street, Chindadripet, Chennai-600002. Ph- 9566065345
Document by Poornima Ramesh
Thursday, February 23, 2017
Paper Dolls and baskets
No comments:
Labels:
Auroville,
basket making,
dolls,
paper craft,
paper machie,
Pondicherry,
recycled craft
Auroville, a place known for its calm and peace with its diversity is also known for its handicrafts. Auroville doesn’t just promote human unity but also helps the struggling craftsmen. With people coming from all over the place, most of them have come there for a progressive conviction of living with no networks they get closer to discovering themselves and their priorities.
Paper Machie is one of the major crafts in Pondicherry that was getting lost in the technological based world. The artisans who had their living based on the craft were moving to other professions due to lack of financial stability. So when an Israeli got interested in it. He decided to invest some money and establish a brand where he employed to help women from that community to gain a better living.
These women now work in the beautiful village near Auroville creating dolls and baskets made out of recycled paper. In the earlier days clay toys were the main attraction but soon craftsmen in Auroville started making toys out of paper which later evolves into baskets and pen holders etc.
The figures of deities were more in demand but these days they make animals and other toys for children. These toys and dolls are colourful as a part of the religious services. The main colours used are orange and red and the accessories are painted on the dolls to make them look rich. Nature, Mythology, folklore these are the themes the craftsmen use to entice the buyers. Now nearly 300 units are involved in the making of paper Machie dolls around in Pondicherry.
The basic technique used in making these dolls are quite simple as they have moulds and the paper which they use to make these dolls are generally newspapers to decrease the cost in making. The baskets are made by rolling the newspapers into a thin roll and pasting them in the right shape on top of another. They are then coated with varnish to stay strong. They don’t paint the baskets as the main aim of the craft is know the beauty of papers that are rolled beautifully into shapes and sizes. Whereas the paper Machie dolls are painted with details.
The making of these dolls takes around two to three days generally. When you walk into the place, it’s filled with colourful that sit beautifully on their shelves and the beautiful baskets in various sizes that are kept. The prices of these are quite expensive as they are a striving community.
Documented by Lakshana vivek
Read More
Paper Machie is one of the major crafts in Pondicherry that was getting lost in the technological based world. The artisans who had their living based on the craft were moving to other professions due to lack of financial stability. So when an Israeli got interested in it. He decided to invest some money and establish a brand where he employed to help women from that community to gain a better living.
These women now work in the beautiful village near Auroville creating dolls and baskets made out of recycled paper. In the earlier days clay toys were the main attraction but soon craftsmen in Auroville started making toys out of paper which later evolves into baskets and pen holders etc.

The figures of deities were more in demand but these days they make animals and other toys for children. These toys and dolls are colourful as a part of the religious services. The main colours used are orange and red and the accessories are painted on the dolls to make them look rich. Nature, Mythology, folklore these are the themes the craftsmen use to entice the buyers. Now nearly 300 units are involved in the making of paper Machie dolls around in Pondicherry.
The basic technique used in making these dolls are quite simple as they have moulds and the paper which they use to make these dolls are generally newspapers to decrease the cost in making. The baskets are made by rolling the newspapers into a thin roll and pasting them in the right shape on top of another. They are then coated with varnish to stay strong. They don’t paint the baskets as the main aim of the craft is know the beauty of papers that are rolled beautifully into shapes and sizes. Whereas the paper Machie dolls are painted with details.

The making of these dolls takes around two to three days generally. When you walk into the place, it’s filled with colourful that sit beautifully on their shelves and the beautiful baskets in various sizes that are kept. The prices of these are quite expensive as they are a striving community.
Documented by Lakshana vivek
Wednesday, February 22, 2017
Korai mat weaving
No comments:
Labels:
carpet,
craft,
eco fiber,
grass mat,
karur,
korai pai,
mat weaving,
textiles,
weaving
The korai mat weaving industry is found across several places in Tamilnadu. In fact such is the diversity, the Mat weaving industry itself is spread and practiced across India in different varied forms. Well known mats include sitalpuri mats, madur mats and of course ‘the korai mats’ made from korai grass. The craft is popular in several places in Tamil Nadu chiefly from Pattamadai and Karur both at the banks of their respective rivers the Thamirabarani and Kaveri. This is because the korai grass plantation can only be done at the banks of waterbodies in marsh lands. This is one of the reasons the korai pai or mats differ from quality and posses different characteristics. Especially, these “mats” or “pais” (as popularly known) pattamadai village are a very famous name from the whole household of “korai pai” family. Because the mats made here are traditionally known for the fine quality. It goes through a very meticulous handwork process which results in silk like quality ultimately earning the name “pattu pai” os silk mats.so, it's a certain fact that pattamadai mats have even registered GI tag for themselves in protection. However, this mat industry plays a crucial role in rural employment and is found in every other possible water body where its potential has been exploited. It is in this way that Karur has naturally established as a secondary korai mat production center taking advantage of rich Kaveri river basin.Apart from these places, korai plantation and mat production is also seen at a lake bank, Puducherry. Hence this establishes the possibilities and platform for diverse variety of mats in market.
Korai belongs to the sedge family of plants, Cyperaceae. They are the chief primary building units of the mats produced. They are grown by farmers as commercial crops on the banks of water bodies. thus, it needs huge water consumption and is entirely depend upon the water body and the quality of water. This plantation is grown in the marshy land for example in Karur the plantations are done along the banks of river Kaveri. The grasses are planted and harvested during the September/October and February/march months.
Location - Karur
The town is located at the bottom of Kaveri river with its other chief mat weaving industry clusters located in villages around 100kms from the town. The plantation field is located in a village called “Mayanur”, which is right at the bank of river Kaveri. Though the korai grass plantation is done along this area, the weaving clusters are located at deep down in other villages. hence this has been a major source of livelihood for many marginalized village folks in every village. “Sinandipatti” is one such village which is also at the same distance from the Karur town. Though these villages are drought ridden and sparsely populated, men here still engage and depend on handloom weaving of mats for the living. one has to take through roads and a frequent public transport is also available.
The industry
Though the industry is climbing small steps success in recent days, but sadly its traditional methods and process of korai pais/mats production are eminent towards extinction. It does not have a large corporate player but instead a more inter connected different take parters in the industry, that is a co operative. There are marketers who give the required orders according to the customer's demand, the farmers cultivate and sell the harvested grass and sell them at required rates and last the weavers who weave a traditional handloom mats. Today the industry sees a large growth machine loom which is electrically powered.This helps in meeting the demands both import and export.
The process
Broadly there are three varieties of mats available in the market. coarse weave, medium, and high-quality weave. The mats produced in the Karur district are primarily coarse variety and the medium one. The process over all has three main steps, harvesting, weaving and finishing. There are other subsidiary steps like dying and wrap thread production. At first, the korai grass are harvested in such way they are cut at the bottom. once harvested they are split into two halves so that they are easy to be woven. Then these harvested and splitter grasses are grouped and laid down flat under the sun for a day so that they get dried up until its colour changes into golden brown apt for weaving.
The dried up korai grasses are transported both power loom and handloom weavers. while for making high-quality soft mats, the production undergoes a tedious process like using only the center pith from the grass which is removed carefully. But this process is not seen Karur clusters as making coarse variety is directly used for weaving. At the parallel, a set of korai grasses are dyed, and the wrap thread is produced naturally from the wild cactus plant “fibers”.
Just like a textile handloom weave, the artisans use a traditional handloom or “kaitheri” to weave perfect handloom weaved mats. It takes weeks to prepare such mats. The artisan who was contacted was rajamuthu,75 years old. He carefully uses his “kichali kuchi” - a stick used to pull a korai grass n place it as a weft. so on he carefully keeps adding on each grass as weft to his mat. this whole process is done by him comfortably sitting in a pit to operate the handloom. On the other hand, there are power loom owners who operate automated machine to produce mats. Here, unlike handlooms( where only cactus plant fibre is used as a wrap) nylon and cotton fibers are also used as a wrap in the weaving process. Along the whole handweaving process, sometimes special orders for marriages are also taken in which the name of the bridegroom is brought into the design.This takes at least two weeks to complete.
The final weaved mats go through the finishing process, where the extra parts around the edges are neatly cut using a large cutter. still, in traditional handmade mats, the edges are cut and stitched strongly with fibre. The finished products are of varied designs. Artisans play with weft and wrap using the dyed grass, which is of three main colors like dark red, indigo and green. Nowadays different products are experimented and are also available in the market like baskets, handbags and much more. The increase in awareness for eco-friendly products also boosts some confidence in the industry.
Contact:
Documented by - Shakti Kumaran SE
Read More
The korai grass
Korai belongs to the sedge family of plants, Cyperaceae. They are the chief primary building units of the mats produced. They are grown by farmers as commercial crops on the banks of water bodies. thus, it needs huge water consumption and is entirely depend upon the water body and the quality of water. This plantation is grown in the marshy land for example in Karur the plantations are done along the banks of river Kaveri. The grasses are planted and harvested during the September/October and February/march months.
Location - Karur
The town is located at the bottom of Kaveri river with its other chief mat weaving industry clusters located in villages around 100kms from the town. The plantation field is located in a village called “Mayanur”, which is right at the bank of river Kaveri. Though the korai grass plantation is done along this area, the weaving clusters are located at deep down in other villages. hence this has been a major source of livelihood for many marginalized village folks in every village. “Sinandipatti” is one such village which is also at the same distance from the Karur town. Though these villages are drought ridden and sparsely populated, men here still engage and depend on handloom weaving of mats for the living. one has to take through roads and a frequent public transport is also available.
The industry
Though the industry is climbing small steps success in recent days, but sadly its traditional methods and process of korai pais/mats production are eminent towards extinction. It does not have a large corporate player but instead a more inter connected different take parters in the industry, that is a co operative. There are marketers who give the required orders according to the customer's demand, the farmers cultivate and sell the harvested grass and sell them at required rates and last the weavers who weave a traditional handloom mats. Today the industry sees a large growth machine loom which is electrically powered.This helps in meeting the demands both import and export.
The process
Broadly there are three varieties of mats available in the market. coarse weave, medium, and high-quality weave. The mats produced in the Karur district are primarily coarse variety and the medium one. The process over all has three main steps, harvesting, weaving and finishing. There are other subsidiary steps like dying and wrap thread production. At first, the korai grass are harvested in such way they are cut at the bottom. once harvested they are split into two halves so that they are easy to be woven. Then these harvested and splitter grasses are grouped and laid down flat under the sun for a day so that they get dried up until its colour changes into golden brown apt for weaving.
The dried up korai grasses are transported both power loom and handloom weavers. while for making high-quality soft mats, the production undergoes a tedious process like using only the center pith from the grass which is removed carefully. But this process is not seen Karur clusters as making coarse variety is directly used for weaving. At the parallel, a set of korai grasses are dyed, and the wrap thread is produced naturally from the wild cactus plant “fibers”.
Just like a textile handloom weave, the artisans use a traditional handloom or “kaitheri” to weave perfect handloom weaved mats. It takes weeks to prepare such mats. The artisan who was contacted was rajamuthu,75 years old. He carefully uses his “kichali kuchi” - a stick used to pull a korai grass n place it as a weft. so on he carefully keeps adding on each grass as weft to his mat. this whole process is done by him comfortably sitting in a pit to operate the handloom. On the other hand, there are power loom owners who operate automated machine to produce mats. Here, unlike handlooms( where only cactus plant fibre is used as a wrap) nylon and cotton fibers are also used as a wrap in the weaving process. Along the whole handweaving process, sometimes special orders for marriages are also taken in which the name of the bridegroom is brought into the design.This takes at least two weeks to complete.
The final weaved mats go through the finishing process, where the extra parts around the edges are neatly cut using a large cutter. still, in traditional handmade mats, the edges are cut and stitched strongly with fibre. The finished products are of varied designs. Artisans play with weft and wrap using the dyed grass, which is of three main colors like dark red, indigo and green. Nowadays different products are experimented and are also available in the market like baskets, handbags and much more. The increase in awareness for eco-friendly products also boosts some confidence in the industry.
Contact:
Documented by - Shakti Kumaran SE
Monday, February 20, 2017
The Art Of Tanjore Painting
No comments:
Labels:
Chennai,
handword,
tanjore painting,
Thanjavur,
thanjavur painting,
traditional painting
One of the most popular form of classical South Indian painting, the Tanjore Painting, is know for its elaborate relief work, dense composition and vibrant colors. It’s surface richness and various embellishments distinguishes it from other types of paintings. The subjects of most of the paintings are Hindu deities and saints. Tanjore Painting gets its name from the ancient pronunciation of the place where it originated, which was then called Thanjavur. It originated during the 16th century, under the reign of the Cholas. Tanjore was the capital of the mighty Chola Empire. The Chola rulers besides being great warriors were builders of magnificent temples and great patrons of arts. It was against this setting that this highly specialized form of art with its characteristically beautiful ornamental relief work flourished. Today, hundreds of dedicated artists, mostly based in Tamil Nadu, India, are keeping this age long tradition alive.
One such artist, Raja, has been practicing this craft for the last 16 years. Working from a tiny room in his house located on south mada road, Thiruvanmiyur, he does the relief work before passing it on to another artist who then adds the gold leaf, color and frames the paintings. Due to the commercialization of the craft, the work is divided amongst artisans to increase the output and reduce the time invested on one painting.
Raja begins the process by smoothening the plywood on which muslin is then stuck using fevicol. A layer of chalk powder mixed with fevicol is applied on the cloth and it is left to dry. It is then coated with arabic gum. After the canvas has been prepped, the drawing is traced on from a gateway sheet to ensure uniformity in the work. Tracing the drawing is also done to save time. Once the drawing is done, depending on whether it’s a flat, semi embossed or 3d embossed, the various layers of chalk powder and plaster of paris are applied. The entire process takes him 2-4 days after which it is packed it thermacol and bubble wrap and sent to the next artist for the further process. The next artist sticks the gold foil on using Arabic gum and then finishes the painting with poster paint. The last thing to be painted on are the god/goddesses eyes as it is believed that once they are painted on the god enters the painting.
A typical Thanjavur painting consists of one main figure, a deity, with a well-rounded body & almond shaped eyes, which is the typical Dravidian structure. This figure is housed in an enclosure created by means of an arch, curtains etc. The painting is bordered and highlighted by the gilded and gem-set technique - a technique used predominantly in all Tanjore paintings, where gold leaves & sparkling stones are used to highlight certain aspects of the painting like ornaments, dresses etc. The paintings are bright & colourful and breathtakingly beautiful.
Over a period of time many changes have occurred in the style and form of painting - for example, the figures are no longer too round, showing the changed preferences in body structures. Presiding deities of various famous temples are also being depicted in the more recent paintings.
The artists lead simple lives even though Tanjore paintings are very expensive as the middlemen make most of the money, paying the artistes a bare minimum. Moreover, artists who have not been trained in the craft have also started practicing it, which reduces its authenticity. People purchase these paintings, as they are cheaper than the authentic ones. Still they continue to put their heart and soul into each painting they make and because of these efforts made by the modern day artists Tanjore Paintings have become the symbol of traditional paintings. One can say that Tanjore painting is one of the finest and the most visually beautiful forms of classical paintings in South India.
Contact
Name - Mr. Raja
Documented by Anushka Harish Salian
Read More
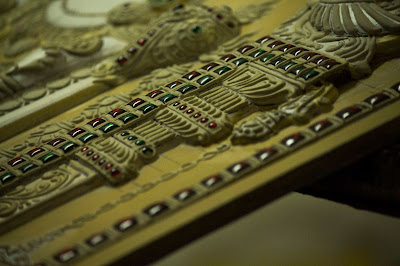
One such artist, Raja, has been practicing this craft for the last 16 years. Working from a tiny room in his house located on south mada road, Thiruvanmiyur, he does the relief work before passing it on to another artist who then adds the gold leaf, color and frames the paintings. Due to the commercialization of the craft, the work is divided amongst artisans to increase the output and reduce the time invested on one painting.
Raja begins the process by smoothening the plywood on which muslin is then stuck using fevicol. A layer of chalk powder mixed with fevicol is applied on the cloth and it is left to dry. It is then coated with arabic gum. After the canvas has been prepped, the drawing is traced on from a gateway sheet to ensure uniformity in the work. Tracing the drawing is also done to save time. Once the drawing is done, depending on whether it’s a flat, semi embossed or 3d embossed, the various layers of chalk powder and plaster of paris are applied. The entire process takes him 2-4 days after which it is packed it thermacol and bubble wrap and sent to the next artist for the further process. The next artist sticks the gold foil on using Arabic gum and then finishes the painting with poster paint. The last thing to be painted on are the god/goddesses eyes as it is believed that once they are painted on the god enters the painting.

Over a period of time many changes have occurred in the style and form of painting - for example, the figures are no longer too round, showing the changed preferences in body structures. Presiding deities of various famous temples are also being depicted in the more recent paintings.
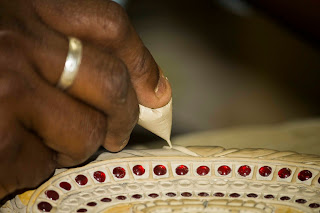
Contact
Name - Mr. Raja
Contact Number - +(91)-9840541546
Address - 48/67a, South mada street, Thiruvanmiyur, Chennai - 600041, Opposite alm Pranav hotel
Documented by Anushka Harish Salian
Sunday, February 19, 2017
Jute Craft of Pondicherry
Jute in India addressed as the “Golden Fibre” is one of the most common raw materials for packaging and for making exquisite craft items. Eco friendly and cheapest known natural fiber, jute has offered global market a chance to bequeath plastic generation a formal good bye. The usage of Jute as a raw material unfurled its existence in the ancient Indian scriptures namely Manu Samhita and Mahabharata. Evidence of the trade of jute cloth in the 16th century still whispers from the pages of history. “Ain-i-akbari” (1590) mentions sackcloth originating from Bengal. The present scenario of jute craft offers a huge inspiration to the jute craft in India and encourages its expansion and demand in abroad. With the progression of time, this established from of jute craft is flourishing in the national and international market.
The jute fibre comes from the stem and ribbon (outer skin) of the jute plant. The fibres are first extracted by retting. The retting process consists of bundling just stems together and immersing them in low, running water. There are two types of retting: stem and ribbon. After the retting process, stripping begins. This job is done mostly by women in the village. In the stripping process, non-fibrous matter is scraped off, then the workers dig in and grab the fibres from within the jute stem.
Jute floor covering consists of woven, tufted and piled carpets. Jute mats and matting with 5/6 meter width and of continuous length are easily being woven in solid and fancy shades and in different weaves like boucle, panama, herringbone etc. jute mats are made both through power loom and handloom in large volume. The traditional Satranji mat is becoming very popular in home décor. Jute non woven are composites are used for underlay, linoleum substrate and more. Jute has many advantages as a home textile, either replacing cotton or blending with it. It is a strong, durable, colour and light fast fibre. Its UV protection, sound and heat insulation, low thermal conduction and anti-static properties make it a wise choice in home décor. Also, fabric made of jute fibres are carbon-dioxide neutral and naturally decomposable. These properties are also why jute can be used in high performance technical textile. Moreover, jute can be grown in 4-6 months with a huge amount of cellulose being produced from the jute hard that can meet most of the wood needs of the world. Jute is the major crop among others that is able to protect deforestation by industrialization. Thus jute is the most environment friendly fibre starting from the seed to expired fibre, as the expired fibres can be recycled more than once.
Contact
The Dharti Jute Craft
100, New Complex, JN Street, Heritage Town, Pondicherry, 605001
www.dartijutecraft.com, contact no-: 0413 222 5533.
Documented by Sonali Islary
Read More
The Dharti Jute craft is a NGO bringing artisans under a unified umbrella for the overall development of the craftsmen.The artisans are provided with training in design and skills development to keep pace with the demands of time and cultural globalization. The villages of Tamil Nadu are full of palm trees, coconut, date and Palmyra. Palm is the major source of raw material for preparing basket and related products. Other raw materials like bamboo, cane, grasses, fibres and reeds are also used in making baskets, thatch ropes, mats.

Jute floor covering consists of woven, tufted and piled carpets. Jute mats and matting with 5/6 meter width and of continuous length are easily being woven in solid and fancy shades and in different weaves like boucle, panama, herringbone etc. jute mats are made both through power loom and handloom in large volume. The traditional Satranji mat is becoming very popular in home décor. Jute non woven are composites are used for underlay, linoleum substrate and more. Jute has many advantages as a home textile, either replacing cotton or blending with it. It is a strong, durable, colour and light fast fibre. Its UV protection, sound and heat insulation, low thermal conduction and anti-static properties make it a wise choice in home décor. Also, fabric made of jute fibres are carbon-dioxide neutral and naturally decomposable. These properties are also why jute can be used in high performance technical textile. Moreover, jute can be grown in 4-6 months with a huge amount of cellulose being produced from the jute hard that can meet most of the wood needs of the world. Jute is the major crop among others that is able to protect deforestation by industrialization. Thus jute is the most environment friendly fibre starting from the seed to expired fibre, as the expired fibres can be recycled more than once.
Contact
The Dharti Jute Craft
100, New Complex, JN Street, Heritage Town, Pondicherry, 605001
www.dartijutecraft.com, contact no-: 0413 222 5533.
Documented by Sonali Islary
Saturday, February 18, 2017
Sea Shell craft of Mahabalipuram
Mahabalipuram is a town situated in the Kanchipuram district of Tamil Nadu, about 60kms from the city of Chennai. The place is infamous for it’s Shore temple and is a major tourist attraction. The town also houses a huge number of Seashells crafts and Rock sculpting shops. A peek into these Seashell craft shops and you will notice that the products mostly comprise of contemporary items such as mirrors adorned with conch shells, seashell curtains, key chains and such. This might give an impression to a common onlooker that the craft is a contemporary one. But the truth is the polar opposite of it.
Mr.P.Babu is one such craftsman who owns a shop near the shore temple. Like every other seashell craftsmen in Mahabalipuram, he too sources most of his shells from wholesalers in Chennai. Most of the sea shells used are fished out from the coastal fisheries of Rameshwaram, Kanyakumari and Cuddalore. They are cleaned and processed here before being sent out to major hubs like Chennai. The Shells are washed and cleaned to remove all the moss and dirt that are stuck to their exterior. This is done in such a way that the shell doesn’t get damaged in the process. After that they are dried in direct sunlight. This helps in getting rid of the soft tissues inside. As the shell is taken from the sea and had been exposed to moss and dirt for a very long time they carry a foul smell. Inorder to get rid of the smell they are soaked in Caustic soda for about thirty minutes. To add shine to the shells they soaked in hot water sprinkled with hydrochloric acid. Finally an emery brush is used to remove some of the irremovable particles.
The local Craftsmen buy their shells from the wholesalers. The small shells are bought in bulk quantities while the bigger and rarer shells are bought on a cost per piece basis. Dyed shells are also available. The smaller shells and cheaper bigger ones are used in making products like wall hangings ,mirror frames, pen stands and other small hand crafted products. The bigger shells are either sold solo or are crafted into much costlier materials like light lamps and such. Mr.Babu assembles wall hangings, mirror frames and other show pieces him selves. He generally uses Fevicol (Adhesive), Glue gun, strings and paints for making his product.Any additional materials depend upon his designs and his designs are limited to his own imagination. He also makes personalised souvenirs by etching names on the shells. He does this by first writing the name on to the shell using a whitener and then mild exposing the entire surface to a very dilute hydrochloric acid. He then finishes by washing it with warm water. He makes all his products in his shop and sells them to the tourists who visit the shore temple.
The sea shells have been in demand for a very long and the craft industry has also existed as long. After Independence because of the advent of science and technology, new chemical compounds have given craftsmen better adhesives and bleaching agents enabling them to come up with new innovations in their crafts. But at the same time shells which that have been used as an ingredient in the making of many materials have been replaced by better alternatives and thus dropped in demand. As the time passed the craftsmen in order to try and impress tourists who are their major customers, started coming with further innovative products but in the process, they have lost their traditional designs. After some time even their designs have become repetitive and stagnant. These craftsmen desperately need help to package, advertise and market their craft to make them unique and noticeable to the foreign market.
Contact details:
Name: P.Babu
Address: Babu Sea Shell Mart
No.55, Beach Road, Mahabalipuram-603104
Mobile no - 9444608144, 9840362097
Working Hours - 10am to 7pm
Documented by Raghavaraj S
Read More

India is a land of rich religious and cultural values. Starting from the birth of a child to the final rites of a family member, the Conch has deep seated roots in the lives of the Indian people. The history of the land is too deep and when the conch got integrated into its culture is unknown. But one can see numerous occurrences of conches in epics and folklores. They have been used by people for ages as ornaments, Religious ceremonies, brandings, tattoos, proverbs, at homes, as feeding pouts, totems, currencies, as horns in the times of war, marriages, incense sticks etc. At present the availability of better adhesives and bleaching agents have enabled the craftsmen to bring innovation to their craft.

Mr.P.Babu is one such craftsman who owns a shop near the shore temple. Like every other seashell craftsmen in Mahabalipuram, he too sources most of his shells from wholesalers in Chennai. Most of the sea shells used are fished out from the coastal fisheries of Rameshwaram, Kanyakumari and Cuddalore. They are cleaned and processed here before being sent out to major hubs like Chennai. The Shells are washed and cleaned to remove all the moss and dirt that are stuck to their exterior. This is done in such a way that the shell doesn’t get damaged in the process. After that they are dried in direct sunlight. This helps in getting rid of the soft tissues inside. As the shell is taken from the sea and had been exposed to moss and dirt for a very long time they carry a foul smell. Inorder to get rid of the smell they are soaked in Caustic soda for about thirty minutes. To add shine to the shells they soaked in hot water sprinkled with hydrochloric acid. Finally an emery brush is used to remove some of the irremovable particles.


The sea shells have been in demand for a very long and the craft industry has also existed as long. After Independence because of the advent of science and technology, new chemical compounds have given craftsmen better adhesives and bleaching agents enabling them to come up with new innovations in their crafts. But at the same time shells which that have been used as an ingredient in the making of many materials have been replaced by better alternatives and thus dropped in demand. As the time passed the craftsmen in order to try and impress tourists who are their major customers, started coming with further innovative products but in the process, they have lost their traditional designs. After some time even their designs have become repetitive and stagnant. These craftsmen desperately need help to package, advertise and market their craft to make them unique and noticeable to the foreign market.
Contact details:
Name: P.Babu
Address: Babu Sea Shell Mart
No.55, Beach Road, Mahabalipuram-603104
Mobile no - 9444608144, 9840362097
Working Hours - 10am to 7pm
Documented by Raghavaraj S
Friday, February 17, 2017
How Sungudi sarees are made
No comments:
Labels:
cotton saree,
craft,
dyeing,
madurai,
saree,
sungudi,
textile design,
textiles,
tie and dye
Woven with the tropical climate in mind and meticulously knotted to give a unique kaleidoscopic effect to each saree the Sungudi of The Temple City, Madurai is generally in great demand among the women folk of South India. The saree is manufactured in the traditional tie or knot dying process. The knots made on the saree are generally evenly spaced with a continuous string running amidst all the knots. Thereafter the saree is dyed with the appropriate colour. Subsequently when the knots are untied the knotted portions remain uncoloured as rings.
The cloth is purchased from a power-loom generally and from a handloom when it’s specified by order only. This cloth is called the ‘Grey Material’, however turns white from grey after washing. The cloth is washed to remove the starch from it. And the cloth is bleached before the technique is started. After which, the designs are made on the cloth after washing and drying the cloth are done by themselves. They combine the traditional designs with contemporary ones also depending on the designs in the market or seasons/ festive occasions.
To make the design it is first marked on the cloth. The designs are first made on paper. The cloth is folded into two halves for knotting the cloth. Approximately around 10,000 to 15,000 knots should be made. This is called as ‘Kai Kattu Sungudi‘ since the designs are made by hand-knotting.
The distance from the pallu to the sari is generally 5 inches and it is 2 inches from the sides. 2 inches gap is mainly to separate the body and the border. The border is measured and marked and squares are drawn within the border to graphically mark the dots to create the desired design. It takes an hour for making the complete grid on the sari. The marking is done only on pure cotton loom.
It is entirely hand crafted hence the design is unique to each saree produced. Thus the design and pattern varies from saree to saree and never is an instance where a a saree has matched another in resemblance.
The marketing of Sungudi sari is limited only to the south because of less awareness of Sungudi as a craft amongst people which makes Sungudi almost extinct in the north. The original tie and dye Sungudi was quite popular and was marketed to most of the South India. As it was a tedious process and less availability of workers made Sungudi lose its originality due to which it was popular. Gradually Sungudi kept on losing its market which resulted in an effort by the people to change the technique of tie and dye to screen printing and batik, which is less tedious as well as quick and gives the same kind of effect. It was after this step Sungudi came back into the market in the form of saris, suit materials, home furnishings.
Today most of the marketing of the Sungudi saris and products are done in local markets, in and around Madurai. During summer season, the sales reaches its peak since the cotton material and its economic range makes it the choice of a large sector of consumers. Due to its affordable prices it is very much bought by the people. During summer the saris are available outside Madurai, in other parts of Tamil Nadu. Sungudi is also supplied to other states of India, mostly in the South.
Sungudi is an explicit art that survives in the land of temples down South India. Problems faced by this craft and people involved can shortly be the reason for its end which is nothing but a loss to the country’s culture. We are bound to get ourselves introduced to the craft, understand its existence, importance and scope for growth.
Contact : Mr A.K Ramesh 9443034187
Documented by: R. Aarthi
Read More

It is believed that the art of making the Sungudi saree came into Madurai during the Nayak dynasty that ruled Madurai around the 16th century onwards. The art of making the Sungudi sarees is time immemorial and came from the weavers. In other words, the Saurashtrian community, who brought it along with them as they migrated into Southern India, perfected the art and gave it the unique blend and style that got it to be distinguished as the Madurai Sungudi Saree. Thus the art is seen to be much older and was known to be practiced since ancient times. And the word 'Sungudi', a Saurashtrian word is derived from the Sanskrit word 'sunnam' meaning 'round'. Thus Sungudi literally meant ringed dots, which are spread throughout the fabric of the Saree and forms a distinct and special feature.
The manufacturing process of the Madurai Sungudi Saree is generally classifiable as a cottage industry. The work commences from the already woven cotton saree that is unbleached. Hence it would be appropriate to say that this is the perfect raw material to which a value-add is made by means of the tie - dyeing. The sarees used are woven using 80's or 100's - combed / carded yarn for warp and 80's - 100's combed/ carded yarn for weft. Pencil markers are used to make grids on the fabric. Cotton yarn is used for tying the knots. Effectively, it takes 10 to 15 days to make a traditional Sungudi saree. Also, the colours used are mainly vegetable dyes. And the water of the sacred River Vaigai, used in the dying process, is believed to possess the unique quality of impacting the brightness of the attractive colours used on the saree making it hold immeasurable worth.

The cloth is purchased from a power-loom generally and from a handloom when it’s specified by order only. This cloth is called the ‘Grey Material’, however turns white from grey after washing. The cloth is washed to remove the starch from it. And the cloth is bleached before the technique is started. After which, the designs are made on the cloth after washing and drying the cloth are done by themselves. They combine the traditional designs with contemporary ones also depending on the designs in the market or seasons/ festive occasions.
To make the design it is first marked on the cloth. The designs are first made on paper. The cloth is folded into two halves for knotting the cloth. Approximately around 10,000 to 15,000 knots should be made. This is called as ‘Kai Kattu Sungudi‘ since the designs are made by hand-knotting.
The distance from the pallu to the sari is generally 5 inches and it is 2 inches from the sides. 2 inches gap is mainly to separate the body and the border. The border is measured and marked and squares are drawn within the border to graphically mark the dots to create the desired design. It takes an hour for making the complete grid on the sari. The marking is done only on pure cotton loom.
It is entirely hand crafted hence the design is unique to each saree produced. Thus the design and pattern varies from saree to saree and never is an instance where a a saree has matched another in resemblance.

The marketing of Sungudi sari is limited only to the south because of less awareness of Sungudi as a craft amongst people which makes Sungudi almost extinct in the north. The original tie and dye Sungudi was quite popular and was marketed to most of the South India. As it was a tedious process and less availability of workers made Sungudi lose its originality due to which it was popular. Gradually Sungudi kept on losing its market which resulted in an effort by the people to change the technique of tie and dye to screen printing and batik, which is less tedious as well as quick and gives the same kind of effect. It was after this step Sungudi came back into the market in the form of saris, suit materials, home furnishings.
Today most of the marketing of the Sungudi saris and products are done in local markets, in and around Madurai. During summer season, the sales reaches its peak since the cotton material and its economic range makes it the choice of a large sector of consumers. Due to its affordable prices it is very much bought by the people. During summer the saris are available outside Madurai, in other parts of Tamil Nadu. Sungudi is also supplied to other states of India, mostly in the South.
Sungudi is an explicit art that survives in the land of temples down South India. Problems faced by this craft and people involved can shortly be the reason for its end which is nothing but a loss to the country’s culture. We are bound to get ourselves introduced to the craft, understand its existence, importance and scope for growth.
Contact : Mr A.K Ramesh 9443034187
Documented by: R. Aarthi
Thursday, February 16, 2017
The Undying Art of Temple Umbrellas
Popularly called the “Gateway to the South India”,Chennai culture is distinctly different from that of any other city in India. Traditional music, dance and all other art forms of Tamil Nadu are very popular in the city. A stroll down the streets of Chintadripet — conceived as a ‘village of small looms’ — and you will see how an old neighbourhood has paused, even if hastily, to take account of time. The neighbourhood is home to a number of heritage structures, including the 19-century CSI Zion Church, the police station, and Chintadripet Higher Secondary School. At least four old temples and families who have been making temple umbrellas and garlands, among other items, for several temples and festivities find a place in the neighbourhood. They claim hereditary rights in making the colourful and elegant umbrellas - Kovil Kudai to dazzle at the Garuda Seva ceremony during the annual brahmotsavam of the world renowned hill shrine of Lord Venkateswara in Tirupati.
But, only about ten to twelve families of artisans based at Chintadripet here are involved in making the umbrellas and have been keeping alive the tradition as the youngsters are no longer attracted to it.
The hand-made umbrellas — excellent pieces of art, are made ahead of the auspicious Tamil month of Purattasi (September-October). This time 13 umbrellas of varying sizes will be sent to Tirupati in a grand procession. The handle, ranging from 7 to 12 feet is made of teak wood, the collapsible parts with cane and the silk-lace work lends charm to the umbrella cover.
“It will take two days to make a small umbrella of seven feet high. Usually, we begin the work after getting orders,” says Kumar, a hereditary artisan. “Only about ten people are involved in making the umbrellas – a tradition passed down to us by our grandfathers,” he adds. These umbrellas are not made by anyone outside their families, Kumar claims. The manufacture is still an intricate handcrafted product. Old traditional ways are still employed. The fingers of many elderly men and women still weave and craft the umbrellas and the design motifs that cover them. Technology has made some of the tasks easier and faster.
Each umbrella is designed with the deity it will be used for. The umbrellas being sent to temples of Vishnu are only in white and redcolor. Those being sent to Siva, Ganesha and Devi temples are multi-colored.The motifs on the umbrella once again find their roots in ancient tradition and stories.
Umbrellas come in many sizes and shapes. There is the flat top to the curved top. The size can be from 4.5 feet to 18 feet. When we see the God or Goddess moving in procession with the huge umbrellas, we truly understand why this ancient art and tradition is still practiced and cherished by the temples and devotees.
Through the ages the making of a temple umbrella has modified and adapted itself to the growing technology and demand. During the olden days only pure silk from Kancheepuram was used to cover the umbrellas today, as the demand for a cheaper and effective umbrella is required materials like satin, velvet and polyester is used. The invent of the embroidery machine plays a big role today as motifs are machine made in a more efficient and faster speed. Even though the evolution has dulled down the actual craft, it is still one of the most respected and sort after South Indian craft. It will always play a major role is various religious processions and ceremonies.
Contact details
Mr. Kumar (Divine temple Umbrellas)
Documented by Vindhya Rk
Read More

But, only about ten to twelve families of artisans based at Chintadripet here are involved in making the umbrellas and have been keeping alive the tradition as the youngsters are no longer attracted to it.
The hand-made umbrellas — excellent pieces of art, are made ahead of the auspicious Tamil month of Purattasi (September-October). This time 13 umbrellas of varying sizes will be sent to Tirupati in a grand procession. The handle, ranging from 7 to 12 feet is made of teak wood, the collapsible parts with cane and the silk-lace work lends charm to the umbrella cover.

“It will take two days to make a small umbrella of seven feet high. Usually, we begin the work after getting orders,” says Kumar, a hereditary artisan. “Only about ten people are involved in making the umbrellas – a tradition passed down to us by our grandfathers,” he adds. These umbrellas are not made by anyone outside their families, Kumar claims. The manufacture is still an intricate handcrafted product. Old traditional ways are still employed. The fingers of many elderly men and women still weave and craft the umbrellas and the design motifs that cover them. Technology has made some of the tasks easier and faster.
Each umbrella is designed with the deity it will be used for. The umbrellas being sent to temples of Vishnu are only in white and redcolor. Those being sent to Siva, Ganesha and Devi temples are multi-colored.The motifs on the umbrella once again find their roots in ancient tradition and stories.

Umbrellas come in many sizes and shapes. There is the flat top to the curved top. The size can be from 4.5 feet to 18 feet. When we see the God or Goddess moving in procession with the huge umbrellas, we truly understand why this ancient art and tradition is still practiced and cherished by the temples and devotees.
Through the ages the making of a temple umbrella has modified and adapted itself to the growing technology and demand. During the olden days only pure silk from Kancheepuram was used to cover the umbrellas today, as the demand for a cheaper and effective umbrella is required materials like satin, velvet and polyester is used. The invent of the embroidery machine plays a big role today as motifs are machine made in a more efficient and faster speed. Even though the evolution has dulled down the actual craft, it is still one of the most respected and sort after South Indian craft. It will always play a major role is various religious processions and ceremonies.
Contact details
Mr. Kumar (Divine temple Umbrellas)
Documented by Vindhya Rk
Wednesday, February 15, 2017
Handmade tiles of Athangudi
No comments:
Labels:
Athangudi tiles,
ceramic,
Chettinadu,
Crafts of South India,
floor tiles,
handmade tiles
Athangudi tiles are the traditional handmade tiles manufactured in Athangudi, a small village in Chettinad region (Sivagangai district), Tamil Nadu for about 160 years. The Chettiars who were traders and land lords imported tiles from the European countries found it difficult to replace them due to the wear and tear of aging. It was expensive to get the spare tiles because of its unavailability. This lead to the setting up of cottages in Athangudi to manufacture the replicas if those tiles which in turn resulted in the creation of tiles that had more vibrant colours and ethnic patterns that gained its own signature resulting in making Athangudi the traditional hub for the production of handmade tiles in Tamil Nadu. Today there are about 500 designs that can be created sing moulds and around 200 designs that could be made in hand. The standard sizes of the tiles 8”X 8”, 10”X 10”, 8” X4” and 8”X 6”. Bigger sizes are also being manufactured if orders are placed.
Athangudi tiles made of synthetic oxides, sand, cement and baby jelly, are prepared through a fascinating process with just bare hands, a clean glass, a metal frame and with or without the mould. Today, a machine that mixes the synthetic oxide with the sand and cement is being which was also once done manually.
The mixture of cement and (coloured) synthetic oxides in a slurry state is poured into different compartments of the moulds which is placed inside the metal frame on the glass. The mould is then removed and the sand is spread over it to fix the colour after which it is concreted with the cement for about an inch. The metal frame is the removed. They are then kept aside in the shade for a day which is then placed in water tank for the curing process. After three days it is kept in the shade to dry and the glasses are removed. Once the tile is completely dry it is ready for the delivery.
The tile needs no machine polishing as it being glazed on by glass. The more you walk on these tiles, the smoother they become. They gain more shine as they age.
These tiles are eco-friendly too as they do not reflect, radiate or conduct heat and have minimal wear and tear. It is believed that the local sand is the secret behind the tiles’ texture. The finish, quality, durability shows the rich craftsmanship. The traditional patterns in vibrant colours are still being created and hence it is among those few choice available even today to create an ethnic ambience.
How to get there: Distance between Chennai to Karaikudi is about 418kms by road. From Karaikudi, there are buses to Athangudi which is about 16kms away from it.
Contact details:
Mr. Natarajan (Sri Ganapathy tiles)
Ponnalazhi Nagar, Karaikudi main road,
Athngudi,Sivagangai-630101
Phone: 04565-281353
Cell: 94874 55929, 94434 66391,97913 74846
Email: sriganapathytiles@gmail.com
Documented by Swathi K
Athangudi tiles made of synthetic oxides, sand, cement and baby jelly, are prepared through a fascinating process with just bare hands, a clean glass, a metal frame and with or without the mould. Today, a machine that mixes the synthetic oxide with the sand and cement is being which was also once done manually.
The tile needs no machine polishing as it being glazed on by glass. The more you walk on these tiles, the smoother they become. They gain more shine as they age.
Contact details:
Mr. Natarajan (Sri Ganapathy tiles)
Ponnalazhi Nagar, Karaikudi main road,
Athngudi,Sivagangai-630101
Phone: 04565-281353
Cell: 94874 55929, 94434 66391,97913 74846
Email: sriganapathytiles@gmail.com
Documented by Swathi K
Subscribe to:
Posts (Atom)